Specialist Tips on Implementing Foam Control in Chemical Handling Environments
Specialist Tips on Implementing Foam Control in Chemical Handling Environments
Blog Article
A Comprehensive Guide to Implementing Foam Control Solutions in Your Procedures
Reliable foam control is a critical element of operational performance that usually goes ignored. Comprehending the ins and outs of foam generation can considerably influence both efficiency and item quality. By examining essential variables such as application compatibility and employees training, organizations can enhance their foam administration efforts.
Recognizing Foam Challenges
Foam obstacles are a considerable issue throughout different sectors, influencing functional effectiveness and product quality. The formation of too much foam can impede procedures such as blending, transportation, and storage space, resulting in increased downtime and waste. In markets like food and drink, drugs, and petrochemicals, foam can hinder production lines, creating product variances and contamination threats.
In addition, foam can block tools performance, resulting in pricey repairs and upkeep. In wastewater treatment, foam can interfere with clarifier procedures, resulting in lower treatment performance and governing conformity concerns.
Comprehending the underlying reasons for foam generation is important for effective monitoring. Factors such as surfactants, temperature level fluctuations, and frustration levels can all add to foam production. Recognizing these elements allows sectors to execute targeted approaches that minimize foam development while maintaining item stability.
Sorts Of Foam Control Solutions

Mechanical remedies involve the use of gadgets such as foam skimmers or defoamers. Chemical remedies, on the various other hand, include the application of defoaming agents-- compounds that disrupt the foam framework, leading to its collapse. Foam Control.
Lastly, functional approaches focus on process modifications. This may involve modifying equipment specifications, such as temperature level and pressure, or transforming the flow prices of liquids to decrease foam generation. Additionally, executing excellent housekeeping methods can additionally minimize foam development by minimizing contaminants that add to foam stability.
Choosing the suitable foam control option involves analyzing the specific needs of the operation, consisting of the kind of process, the qualities of the materials included, and safety factors to consider.
Choosing the Right Products
Picking the ideal foam control products calls for a thorough understanding of the certain application and its distinct challenges. Elements such as the kind of foam, the atmosphere in which it happens, and the desired end result all play essential functions in product selection. Foam Control. For example, in sectors like food handling, it is imperative to pick food-grade defoamers that follow security regulations while efficiently managing foam.
Furthermore, take into consideration the thickness of the fluid where the foam trouble exists. Some items are created for low-viscosity applications, while others are tailored for thicker liquids. Compatibility with existing procedures is an additional critical facet; the picked foam control agents should integrate effortlessly without interfering with overall procedures.
An additional critical element is the method of Recommended Site application. Some items may require dilution, while others can be used straight. Assessing the simplicity of usage and the required dosage can provide understandings into the item's performance and cost-effectiveness.
Execution Methods
Effective application strategies for foam control options need a systematic method that aligns product selection with functional requirements. The primary step entails an extensive evaluation of the processes where foam occurs, identifying certain areas that require treatment. By involving cross-functional groups, including manufacturing, design, and high quality assurance, companies can collect understandings that educate the choice of one of the most reliable foam control items.
Next, it is essential to develop clear purposes for foam decrease, making certain that these goals are quantifiable and attainable. This might include defining acceptable foam degrees and the timelines for execution. Educating employees on the residential or commercial properties and application approaches of picked foam control representatives is equally vital, as proper use is vital for optimal results.
Furthermore, integrating foam control services into existing process needs mindful preparation. Organizations must create a phased implementation strategy, permitting changes based upon initial end results. Normal communication and responses loopholes with staff associated with the process will assist in prompt analytical and promote a culture of constant renovation. Ultimately, a well-structured strategy will boost functional efficiency while efficiently handling foam-related obstacles.
Surveillance and Assessing Efficiency
Monitoring and assessing the performance of foam control options is necessary for making certain that executed strategies produce the preferred outcomes. This procedure includes systematic data collection and analysis to analyze the efficiency of foam control representatives and strategies. Key efficiency indicators (KPIs) need to be established before application, permitting a clear standard against which to measure progression.
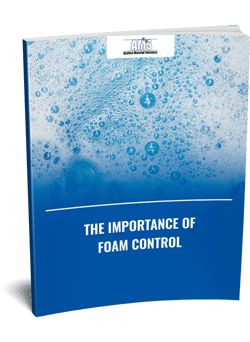
Assessing check my site performance additionally needs regular testimonials of foam control treatments and agent efficiency. This can be accomplished via tasting and testing, enabling drivers to establish if existing remedies are meeting functional demands. It is vital to obtain responses from group members that interact with these systems daily, as their insights can reveal operational nuances that quantitative information may overlook.
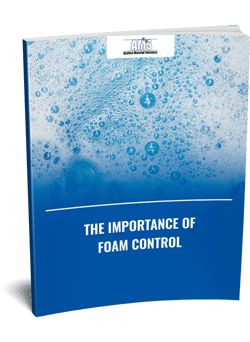
Inevitably, an organized tracking and analysis structure helps identify essential changes, ensuring that foam control options stay reliable, inexpensive, and lined up with business goals.
Conclusion
In verdict, effective foam control options are vital for optimizing functional performance and maintaining product high quality. A complete understanding of foam obstacles, integrated with the selection of ideal items and implementation strategies, helps with the successful management of foam generation.
Applying excellent housekeeping methods can also mitigate foam formation by lowering impurities that add to foam stability.
Choosing the best foam control products calls for a complete understanding of the particular application and its special obstacles (Foam Control).Effective application approaches for foam control options require a systematic method that straightens product choice with operational requirements.In verdict, reliable foam control options are important for enhancing functional performance and keeping item quality. A comprehensive understanding of foam obstacles, combined with the selection of proper try this out products and implementation techniques, assists in the successful management of foam generation
Report this page